钛及钛合金由于具有比强度高.抗腐蚀性好、耐高温等一系列突出优点.使其发展成为现代航空航天工业中广有前途的金属结构材料121。自从20世纪50年代美国首次将Ti-6AI-4V钛合金螺栓应用于B-52型轰炸机上,并取得了非常好的减重效果后,各航空工业发达国家都纷纷展开了钛合金紧固件的研究及工程应用。
钛合金紧固件代替大部分比强度较低的钢制紧固件后,对飞行器减重取得非常显著的效果。如波音747飞机紧固件以钛代钢后,其结构质量减轻了1814 kg;俄罗斯的伊尔-96飞机,一架用14.2 万件钛合金紧固件,较钢!件重量减轻达600kg;一架图204飞机上采用940kg的BT16钛合金紧固件,较钢件减轻688kg。钛合金的正电位性能恰好与碳纤维复合材料相匹配,有效地防止了紧固件的电偶腐蚀.使钛合金成为复合材料的最佳连接材料。因此,随着先进军民用飞机钛合金和复合材料用量的不断增加,对钛合金紧固件的需求日益增加。钛合金比铝合金的使用温度高出150-200C,对于在飞行器结构中因工作温度过高而不能采用铝合金紧固件的部位,钛合金将是-种更好的选择。此外.钛合金所固有的良好弹性和无磁性,对防止紧固螺栓的松动和防磁场干扰也具有非常重要的作用附7。
在美国军民用飞机上,钛合金紧固件已基本取代了合金钢紧固件。国外钛合金紧固件的应用已经非常普遍,大型民用飞机单机钛合金紧固件的用量达到数十万件,同时各类新型的钛合金紧固件也被不断地研制开发出来凹。我国钛合金紧固件的研制历史可追溯到1965年,成都飞机设计研究所根据新机需要提出研制钛合金铆钉.20世纪70年代相关单位进行了钛合金铆钉及应用研究工作.20世纪80年代在我国部分第二代军用飞机上开始少量使用钛合金铆钉、螺栓等紧固件89。20世纪90年代后期,随着国外第三代重型战斗机生产线的引进和国产第三代战斗机的研制,以及大最航空转包生产业务的开展.我国航空工业中开始使用一些钛合金紧固件。近年来随着我国航空航天工业的发展.国内相关单位有针对性地开展了大量基础材料与紧固件制造技术方面的研究开发工作,目前我国自主研制生产的钛合金紧固件已经在我国的改型飞机和新设计的飞机中获得了大量工程应用。
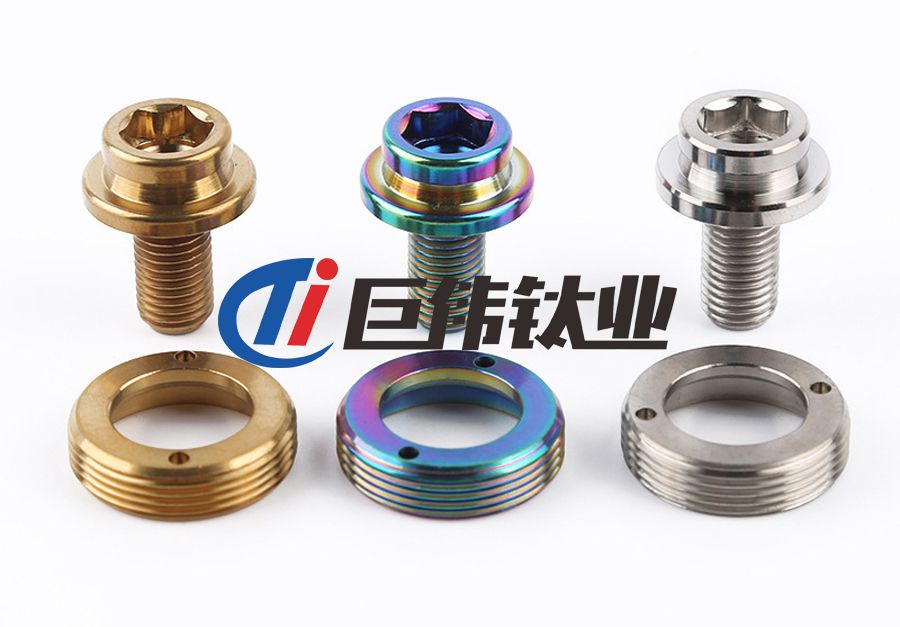
1、铆钉类紧固件用钛合金材料
航空航天工业中常用的紧固件主要包括铆钉、螺栓及特种紧固件3大类。对铆钉来说,最重要的是材料的冷态塑性.只有冷态塑性好的材料制造的铆钉,才能够
进行冷铆接安装。通常在对强度要求不太高而对耐蚀性能要求高的部位采用钛合金铆钉, β型钛合金由于在固溶状态下为单一的晶粒、 且由于其具有体心立方的原子结构排列.所以该类合金具有十分优异的冷加工性能,非常适用于制造钛合金铆钉。
1.1 TB2钛合金
我国钛合金紧固件的研制就是以TB2钛合金铆钉的研制工作为起点的。1965 年,成都飞机设计研究所在新机研制时提出.计划在其后机身钛结构件上采用钛
合金铆钉,并提出了论证和设计。从1970年开始,在天津冶金局材料研究所和有色金属研究院等单位的配合下,成都飞机设计研究所与成飞公司联合展开了TB2钛合金铆钉的研制及应用研究工作,先后完成了TB2钛合金材料研制、丝材冷镦成形研究、铆钉铆接试验研究等工作,并于1979年完成了相关工作技术鉴定,制订了暂行技术条件图。TB2 钛合金是-种亚稳定型β钛合金,合金名义成分Ti-3AI-8Cr- -5Mo -5V。该合金在固溶处理状态下具有优异的冷成形性能和焊接性能,我国目前主要用作制造卫星波纹壳体、星箭连接带及各类冷镦铆钉,有时也用于小规格螺栓的制造。制造航空紧固件时, 其使用温度一般在300C以下,航天紧固件可在短时间内使用到500C中。
1986年,我国颁布了第一部钛合金紧固件专用标准CJB120-1986《钛合金铆钉》.1990年我国颁布了第2部及第3部钛合金紧固件专用技术标准CJB856- _90%抗拉型钛合金环槽铆钉规范》与GJB857.1- -90《1000沉头抗拉型钛合金进环槽铆钉》这3部标准都是TB2钛合金铆钉的专用技术标准.就各类规格的TB2铆钉进行了明确规范,为其工程化批产及应用奠定了标准基础。目前TB2制造的钛合金铆钉已经在我国航天工业中的多个型号获得了大量应用,同时在航空型号产品中也获得了一定数量的应用,均取得了良好的效果13-1。
1.2 TB5钛合金
TB5钛合金是- -种亚稳定β型钛合金,其名义成分为Ti-15V-3Cr-3Sn-3Al。该合金最初是在美国空军的资助下开发的.由洛克希德.马丁公司确定成分、TMET公司进行规模化生产。该合金具有优异的冷成形性能,其冷成形能力与纯钛相当,可在固溶状态下进行各种复杂零件的冷成形(如铆钉铆接),时效后室温拉伸强度可达1000MPa以上,该合金由于其V元素含量高,抗氧化性能较差,-般在200C以下的工作环境中使用,但是该合金具有优异的抗腐蚀性能间。
美国普惠公司在其生产的航空发动机上大量使用Ti-15V-3Cr-3Sn-3AI钛合金作为托架,美国B-1B轰炸机上Ti-15V-3Cr- 3Sn-3A1钛合金零件的用量达到1000多个,Ti-15V-3Cr- 3Sn- 3AI钛合金紧固件在波音飞机上也应用了很多年网。我国使用TB5钛合金替代30CrMnSiA制造某歼击机伞梁以及制造卫星发动机波纹板等部件。同时采用TB5钛合金制造与歼击机伞梁和卫星波纹板配套使用的冷镦铆钉凹。
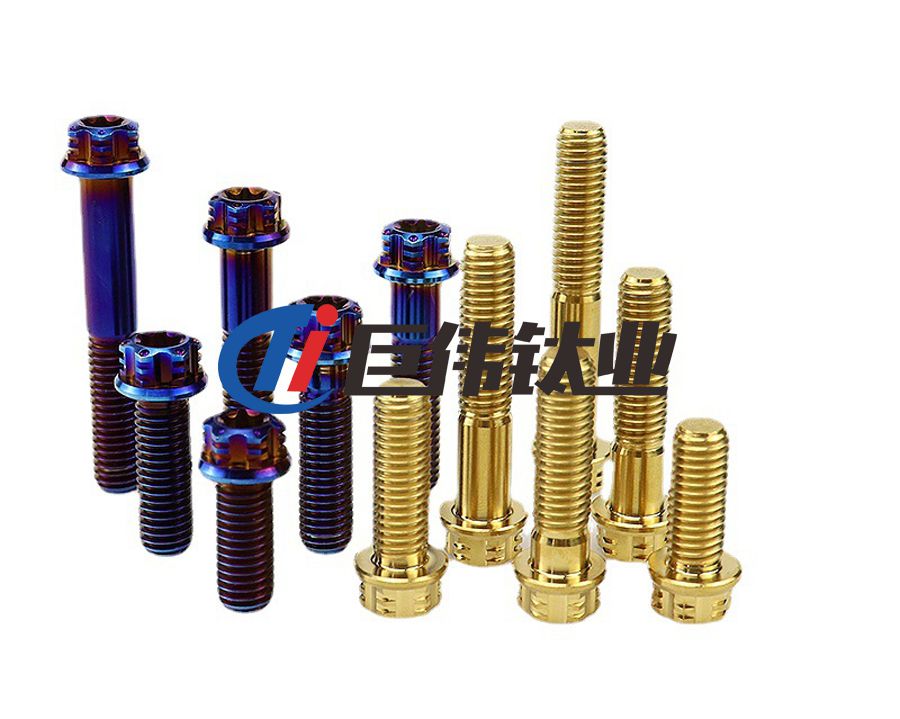
1.3 Ti-45Nb合金
Ti-45Nb合金作为一种铆钉专用材料,其突出的优点是塑性高(伸长率可达20%以上,断面收缩率高达60%-80%),冷加工性能优异,其剪切强度(τ≥350MPa)和抗拉强度(σ。≥450MPa)均高于纯钛,并且冷变形抗力低于纯钛,非常适合做复合材料连接用铆钉材料。美国针对Ti-4SNb合金进行了大量的基础研究工作.研制技术较为成熟,并于1974年列人AMS4982规范,2002年修订为AMS4982C,至今获得广泛使用。美国在航空航天铆钉产品中,Ti-45Nb合金已经全面取代纯钛。该合金与Ti-6AI-4V合金搭配,.制成的双金属铆钉,已经在空客和波音飞机上获得大量应用17-19%。
对于要求剪切强度高在安装过程中不允许铆钉杆变形的铆钉,一般采用双金属钛合金铆钉,双金属钛合金铆钉是由Ti-6AI-4V钉杆和Ti-4SNb头部组成.经过惯性摩擦焊接.紧密融合在一起而形成了一个整体实心铆钉。这种双金属铆钉在铆接时,只需用较小的冲击力就可以使Ti-45Nb铆钉头产生塑性变形,而Ti-6AI-4V铆钉杆却不变形。双金属钛合金铆钉在B-1轰炸机、波音等飞机上广泛用于钛合金构件及复合材料构件的铆接。如美国F-14战斗机机翼前缘使用4000只该双金属铆钉.其疲劳性能与高锁螺栓相当,而成本可降低50%,重量轻30%-40%.这种双金属铆钉的成本要低于其他β型钛合金铆钉。近年来我国也相继研制开发了该型双金属铆钉和Ti- 45Nb铆钉,已经在新一代飞机的复合材料蒙皮铆接中获得了工程应用。
2、螺栓类紧固件用钛合金材料
航空航天紧固件中使用量最大的是钛合金螺栓,钛合金螺栓按其用途可分为普通螺栓高锁螺栓及干涉型螺栓等。以来制造螺栓的钛合金材料, -般要求其热处
理后获得高的抗拉强度和剪切强度.通常要求其强度水平与30CrMnSiA高强度合金钢相当12。
2.1 TC4钛合金(。≥1100MPa级)
TC4 (美国牌号Ti-6AI-4V )钛合金最初由美国在1954年首先研制成功,目前已经发展成为一种国际性的钛合金.是目前人们对其研究最为全面、最为深入的钛合金。在航空、航天、民用等工业中得到了广泛应用。已经广泛用于制造飞机结构中的梁、框、起落架、紧固件.航空发动机风扇、压气机盘、机匣、叶片等,同时也大量用于其他行业中,目前占钛合金产量的一半以上。该合金具有良好的工艺塑性和超塑性,合金a+BIp转变温度980~- 1010C,长期工作温度可达400C。1973年开始,为配合涡扇-8航空发动机TC4钛合金叶片的研制工
作,我国开始了该合金的研究与工程应用121956年,美国采用TC4 (Ti-6A1-4V )钛合金制造了当今世界上第一批钛合金螺栓,首先用在B-52轰炸机上(代替原3erMnsiA螺栓),由于使用效果非常好,很快就被推广应用.现在西方几平所有的飞机都在大量采用TC4 mlAY 41)社合金制造其螺栓。但是由于TC4 (Ti-6A144V)是α+ β叙相合金,不能冷锻成形、其钉头必须加热镦制.热处理需真空水淬和时效,对加工设备及工艺要求高。20世纪80年代后期,我国相关单位开展了TC4钛合金紧固件热镦技术研究,先后开发出了热镦机床,与20世纪90年代实现了TC4钛合金紧固件的工业化生产。目前我国多个航空航天标准件厂
都具有批量生产TC4螺栓的热镦设备与技术能力,采用TC4钛合金制造的螺栓已经在我国新一代军机、航天飞行器、卫星中获得了大量工程应用126.10.2%。
2.2TC6钛合金(α≥980MPa级)
为满足航空发动机高温使用要求.北京航空制造工程研究所研制出了可耐500 C以下高温的TC6 (俄罗斯材料BT3-1)钛合金紧固件,与TC4钛合金相比,该预材料对温度具有较高的敏感性,其紧固件制造更困难。该合金是前苏联研制的BT3-1钛合金,名义成分为Ti-6A1-2.5Mo-1.5Cr-0.5Fe-0.3Si,目前在俄罗斯得到广泛应用2。我国在1979年为配合WP13航空发动机TC6钛合金尾杆等部件及配套紧固件的研制工作,进行了该合金的仿制工作及应用研究工作。TC6合金是一 种综合性能良好的马氏体型α+β型双相钛合金,一般在退人状态不使用也可进行适当的热处理强化。该合金具有良好的性能,抗氧化性能和耐腐蚀性能非常优异,其制造的零部件可在400C下长时间工作600h以上.450tC中P长时间工作2000以上。等温退火处理后室温抗拉强度大于980MPaJ届服强度C大于840MPa、延伸率大于10%、断面收缩率大于25%。400C高温拉伸强度大于720MPa、延伸率大于14%、断面收缩率大于40%。为了进一步提高其使用强度.也可进行“固溶+时效"处理日。
2.3 TC16(σ。≥1030MPa级)
目前对于钢制紧固件,大部分都采用冷镦成形加工,只有少数尺寸较大的采用热镦成形加工,冷镦工艺使紧固件实现了大批量连续生产。但是大部分工业钛
合金由于冷成形性能差.无法进行冷镦成形加工。因此,在西方国家,TC4钛合金紧固件主要采用热镦成形工艺方法生产.热镦工艺的缺点在于:坯料加热时易出现局部烧伤和过热以及表面氧化,同时不易实现自动化连续镦制、生产效率低。为了提高钛合金紧固件生产效率及其质量的稳定性.前苏联研制开发了紧固件专用冷镦用BTI6钛合金,实现了钛合金紧固件冷镦技术的发展和跨越.并在伊尔76伊尔86.伊尔96、安124.Su27系列等苏制(俄制)飞机上获得了大量工程应用1.27。BT16 (我国仿制牌号TC16)钛合金名义成分Ti-3AI- -5Mo -4.5V,该合金是马氏体型ax+β型双相钛合金,β稳定系数为0.83,接近临界成分。该钛合金主要用于制造工作温度350C以下的航空紧固件,合金a+β/β转变温度( 860+20) C。较小的β晶粒和在退火状态下高达25%的β相体积分数决定了BT16合金具有优异的室温工艺塑性,所以该合金可在室温条件下完成紧固件头部的冷镦成形,因而明显提高了其螺栓生产效率、降低了生产成本.随后在固溶时效热处理后其强度可达1030~1 180MPa。俄罗斯(前苏联)钛合金螺栓类紧固件主要采用BT16钛合金制造.使用了几十年没有出现任何质量事故。我国20世纪90年代从俄罗斯引进了Su-27飞机生产线(为了满足Su- -27飞机的国
产化需求,国内相关单位随即开展了BT16钛合金及其紧固件的国产化工作!我国仿制后命名为TC16钛合金。有前我国自主研制生产的Te16钛合金螺栓已经在国产的第三代战斗机上获得了大量工程应用P1.2。
2.4 TB3(o。≥1100MPa级)
20世纪七八十年代,美国等西方工业发达国家的航空航天用1100MPa级钛合金螺栓主要采用TC4 (Ti-6AI-4V )钛合金材料制造,都是采用热镦成形工艺生产。我国20世纪70年代末80年代初应复合材料结构连接需求,急需1100MPa的钛合金螺栓类紧固件,由于受到热镦设备的限制(当时国内没有热镦成形设备),无法研, 制生产100MPa级的TC4 (Ti-6AI-4V )螺栓,为此主要集中精力研制可以直接冷镦的β型钛合金, TB3钛合金就是在这种背景条件下研制开发出来的。TB3合金的成分设计参照了美国钛金属公司20世纪研制开发的Ti-8Mo- -8V-2Fe- 3AI钛合金。
TB3钛合金是一种可热处理强化的亚稳定β型钛合金. 合金名义成分为Ti-10Mo-8V-1Fe- 3.5Al。该合金的主要优点是固溶处理状态具有优异的冷成形性能,其冷镦比( D/D。)可达2.8,“固溶+时效"制度处理后可获得高的强度.主要用于制造使用温度低于300C的1100MPa级高强度航空航天紧固件。1982年10月,我国开始了TB3钛合金螺栓的研制工作,1985年研制工作取得进展.并形成了相关技术规范。在20世纪80年代中后期国产TB3钛合金先后制成高锁螺栓和干涉型螺栓,装于飞机复合材料结构与金属结构,为我国钛合金螺栓类紧固件的应用摸索出了二定经验基础。该合金现已广泛用做1100MPa钛合金螺栓的制造,并已成功应用于Y-7. J-8、J-10 飞机及某些航天飞行器上。
目前,TB3钛合金已成为我国能够工业化生产的宇航飞行器用钛合金螺栓类紧固件的主要材料。同时,该钛合金也用于铆钉的制造.我国在2006年颁布的CJB120-2006《钛及钛合金铆钉》中也将TB3钛材作为铆钉用料正式列人标准12.231。
2.5 TB8钛合金( σp≥1280MPa级)
随着航空航天技术的飞速发展,在军民用飞机上所采用的机械连接技术要求越来越高,其所采用的标准件技术含量也越来越高,其在整机上所起的作用已不仅是“紧固"、“连接”作用,而是成为实现整机性能的重要结构件。未来航空航天技术的发展趋势要求新型紧固件的比强度高,即要求重量轻、强度高。所以美国、俄罗斯、法国等世界航空强国都在积极开发抗拉强度1200MPa以上的高强度钛合金材料及其紧固件。近年来,美铝公司开发出了Timetal555钛合金高强螺栓.其固溶时效后抗拉强度达1300MPa以上、双剪强度大于745MPa.延伸率大于10% .各项性能指标完全达到了典型的1250MPa镀镉合金钢紧固件规范的要求。SPS 航空紧固件集团采用SPS TITANTM761钛合金加工制造的螺栓产品Aerlite180,其抗拉强度可达1240MPa剪切强度可达745MPa,达到了许多合金钢和耐蚀合金紧固件的强度水平.同时减重40%。
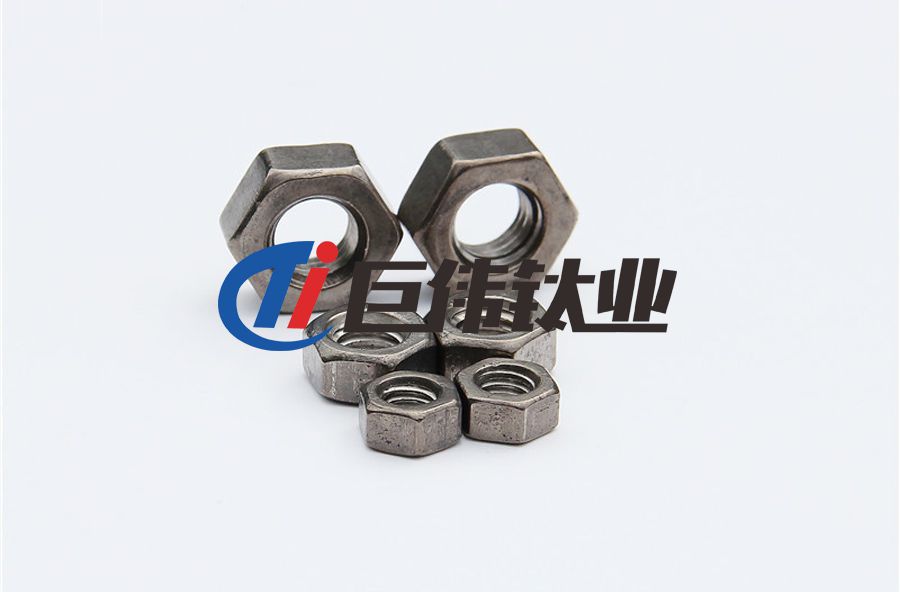
为了紧跟国际先进航空航天钛合金紧固件发展趋势,近年来西工大超晶公司与信阳航天标准件厂联合研制开发了紧固件专用TB8钛合金棒丝材及其1280MPa高强螺栓类紧固件,其规格从φ4~φ25。TB8钛合金是我国仿制美国的β21S钛合金,其名义成分为Ti-3AI-2.7Nb-15Mo, β2IS合金是美国钛金属公司( Timent ) 1989年为NASP计划研制开发的亚稳定β型钛合金,β21S钛合金具有优异的冷热加工性能、深的淬透性、高的抗蠕变性能、高的抗氧化性能和良好的抗腐蚀性能,所以该合金得到了飞机设计者和制造者的认可.作为优良的宇航结构材料于1994年首先被列人美国的ASTM标准中,美国主要使用该合金制造航天飞机用钛基复合材料及波音777等飞机发动机吊舱部件。我国从20世纪90年代开始进行了该合金的仿制工作,完成了某型飞机结构件用TB8钛合金锻件及钣金件的研制及应用研究工作,由于最终没有获得工程化应用,仅在CB/T3620.1-2007《钛及钛合金牌号和化学成分》中对其牌号及成分进行规范.其材料及产品没有形成国标、国军标以及航标规范132期。
信阳航天标准件厂与西工大超晶公司联合研制开发的1280MPa级TB8钛合金螺栓实物照片见图1,主要性能指标见表1。由于该合金的采用的β稳定元素为高熔点、抗氧化的钼元素和铌元素,而非TB2. TB3钛合金采用的抗氧化性能差的钒元素,所以该合金制造的紧固件长时间使用温度可达550C,彻底解决了传统高强B钛合金紧固件使用温度低(不高于300C)的问题。目前,研制开发的该1280MPa级TB8钛合金高强螺栓已经在我国新一代飞机中获得了工程应用,取得了良好的减重效果和与复合材料相容性效果。
3、总结
可以看出,航空用钛合金紧固件的研究与应用自工业钛合金出现就已经开始,美国.俄罗斯(前苏联)等航空工业发达国家在很早就已经形成了符合自身工艺技术的紧固件用钛合金材料体系,钛合金紧固件已经在其航空制造领域获得了大量应用。而我国航空用钛合金紧固件的研究及应用起步较晚,都是在航空发动机或飞机的仿制、技术借鉴或引进改进过程中被动进行的,制造紧固件的钛合金材料基本都是借鉴或仿制俄罗斯(前苏联).美国的,同时我们国家航空紧固件中钛合金紧固件的占有量相对较低。随着我国航空工业的迅速发展及对~飞行器性能要求的不断提高,未来高性能航空紧固件对其制造钛合金材料提出了更高强度.更高断裂韧性、更高疲劳性能要求。
相关链接