近年来,随着全球经济技术的高速发展,产品的多功能化和轻便化的不断推进,使得薄膜科学的应用日益广泛。而溅射靶材作为锻膜产业的基本耗材, 其制备技术也得到了长足发展 。溅射薄膜由于其致密度高 ,附着性好,被广泛应用于装饰、玻璃、电子器件、光学器件、 半导体、磁记录、平面显示屏 、太阳能电池、飞机叶片防护涂层等众多领域。随着上述领域的快速发展, 对靶材的需求量急剧增加, 同时对靶材的高质质量、大型化及利用率方面也提出了更高的要求。

一、溅射靶材的特性要求
为了提高溅射效率和确保沉积薄膜的质量,对溅射靶材特性有如下要求。
1、纯度
高纯度是对溅射靶材的一个基本特性要求。靶材的纯度越高,溅射薄膜的 性能越好。一般溅射靶材的纯度至少需要达到99.95%。溅射靶材作为溅射中的阴极源, 固体中的杂质和气孔中的氧气和水气是沉积薄膜的主要污染源。
2、致密度
溅射镀膜的过程中,致密度较小的溅射靶受轰击时, 由于靶材内部孔隙内存在的气体突然释放 ,造成大尺寸的靶材颗粒或微粒飞溅 ,或成膜之后膜材受二次电子轰击造成微粒飞溅。这些微粒的出现会降低薄膜品质。为了减少靶材固体中的气孔,提高薄膜性能 ,一般要求溅射靶材具有较高的致密度。对溅射靶材而言 ,其相对密度应该在98%以上。
3、晶粒尺寸及尺寸分布
通常溅射靶材为多晶结构,晶粒大小可由微米到毫米量级。试验研究表明 ,细小尺寸晶粒靶的溅射速率要比粗晶粒快;而晶粒尺寸相差较小的靶,淀积薄膜的厚度分布也较均匀。
4、结晶取向
由于溅射时靶材原子容易沿原子六方最紧密排列方向择优溅射出来,因此,为达到最高溅射速率,常通过改变靶材结晶结构的方法来增加溅射速率。
靶材的结晶方向对溅射膜层的厚度均匀性影响也较大。 因此,获得一定结晶取向的靶材对薄膜的溅射过程至关重要。
5、靶材与底盘的绑定
一般溅射靶材溅射前必须与无氧铜、 不锈钢或铝等其他材料的底盘连接在一起,使溅射过程中靶材与底盘的导热导电状况良好。绑定后必须经过超声波检验,保证两者的不结合区域小于2%, 这样才能满足大功率溅射要求而不致脱落。
二、溅射靶材的主要制备方法
溅射靶材按其材质可分为纯金属靶、合金靶、陶瓷化合物靶(包括氧化物、 硅化物、 碳化物、 硫化物等)复合靶。按形状可分为平面靶和管状旋转靶,平面靶又可分为矩形板和圆形靶。 目前, 虽然溅射靶材种类繁多但其基本的制备工艺主要包括粉末冶金法和熔炼铸造认两大类 , 但随着技术装备的不断进步, 大功率的热喷涂技术也逐步在靶材生产中得到了应用。
1、粉末冶金方法
粉末冶金法包括粉末压制烧结法、粉末热等静压等。粉末冶金法是将粉体原料按比例混合均匀, 经过压制成形, 然后在高温下烧结, 经压力加工、热处理后最终得到靶材。该类力法适合于难熔金属如钨、钼靶材及陶瓷靶材的制备。粉末冶金法制备溅射靶材时, 其关键于(1)选择高纯粉料作为原料; (2)选择能实现快速致密化的成形烧结技术,以保证靶材的低孔隙率,并控制晶粒度; (3)制备过程严格控制杂质元素的引入。采用粉末冶金法制备的靶材具有成分均匀及晶粒均匀细小、成品率高的优点, 但制备过程采用粉末混合、压制和烧结工艺,容易在制备过程中带入杂质元素, 烧结过程杂质排除效果较差, 造成靶材纯度相对较低, 并且烧结靶材的密度也较熔炼靶低。
2、熔炼铸造法
熔炼铸造法的基本工艺是将一定比例的合金原料熔炼后浇注到模具中形成铸锭, 然后通过锻造、挤压或拉拔等成形工艺进行加工, 最后经过热处理、机加工等工序制备得到溅射靶材。常用的熔炼力法有真空感应熔炼,直空电弧熔炼和真空电子束熔炼等。与粉末冶金法相比,熔炼铸造法得到的靶材纯度高. 密度高, 但其工艺较为复杂对设备要求高, 成本也随之升高。并且靶材晶粒粗大。若各组分之间熔点和密度相差较大, 则难以获得成分均匀的合金靶材。
3、等离子喷涂方法
等离子喷涂是将金属或非金属材料粉末送入等离子射流中, 利用等离子火焰加热融化喷涂粉末, 并在冲击力的作用下将其沉积到基体上, 从而获得具有各种功能的靶材。
三、等离子喷涂方法制造管状旋转靶材
在平面磁控溅射过程中, 由于正交电磁场对溅射离子的作用关系,溅射靶在溅射过程中将产生不均匀冲蚀现象,从而造成溅射靶材的利用率普遍不高, 约30%左右。近年来虽然通过设备改造可相应提高靶材的利用率,但也只有50%左右。另外, 靶材原子被氩离子撞击出来后,约有1/6的溅射原子会淀积到真空室内壁或支架上,增加清洁真空设备的费用及停机时间。因此,提高靶材利用率的关键在千实现溅射设备的更新换代。另外一种提高溅射靶材利用率的方法是采用管状旋转靶材。相比平面靶材, 采用旋转靶结构的设计显示出它的实质性优势。从平面靶到旋转靶在几何结构和设计上的变化增加了靶材的利用率, 利用率从平面靶的30%~50%可增加到旋转靶的>80%。此外,如果以溅射功率乘以溅射时间来衡量靶材料的寿命,则旋转靶的寿命要比平面靶长5倍。由于旋转靶在溅射过程中不停地旋转, 所以在它的表面不会产生重沉积现象。
以传统的粉末冶金和熔铸方法在溅射靶材的制备方面虽然被广泛采用, 但其共同的问题就是难以制备大尺寸(平面靶及管状靶)的溅射靶材, 尤其对一些高熔点脆性材料更是如此。而靶材的大尺寸及高利用率的旋转靶材巳经成为了未来锁膜领域的新趋势。因此,开发新型的大尺寸旋转溅射靶材制备方法已经成为目前靶材制备领域亟待解决的问题。
1、等离子喷涂技术原理
等离子喷涂是利用等离子火焰加热融化喷涂粉末使其形成涂层, 一般等离子喷涂使用Ar或N2气, 再加入5%~10%的H2气,气体进入电极区的弧状区被加热电离形成等离子体, 其中心温度一般可达15000℃以上, 将金属或非金属材料粉末送入等离子射流中, 将其加热到半熔化 、 熔化或气化状态, 并在冲击力的作用下将 其沉积到晶体上,从而获得具有各种功能的靶材( 如图 1) 。
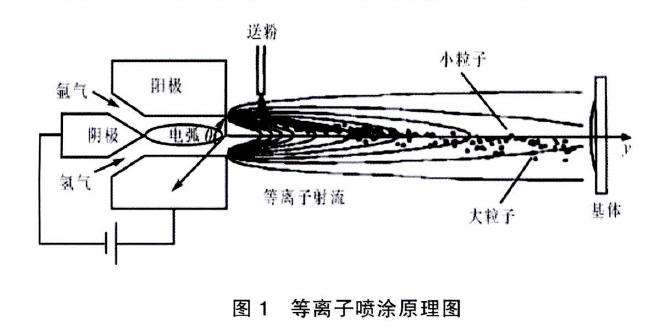
2、等离子喷涂技术的特点
等离子喷涂具有如下特点:(1)等离子喷涂的焰流温度高, 热量集中, 几乎能融化所有高熔点的粉末材料, 可以根据工件表面性能要求制备出各种性能的涂层;(2)等离子焰流喷射速度高 , 能使粉末获得较大的动能和较高的温度,涂层与基体结合强度高;(3)喷涂层平整光滑,厚度精确可控,直接进行精加工即可获得产品,是一种净尺寸成形制备方法 , 节省材料 , 特别适合贵重金屈涂层及靶材的制备;(4)等离子喷涂通过采用真空密闭, 通入还原性 气体、惰性气体保护等方法, 可获得氧含量低、杂质少的涂层; (5) 采用高能等离子喷涂设备 、粉末沉积率高,沉积速度快, 可获得较厚的涂层, 这是制备溅射靶材的重要保证。
3、等离子喷涂设备
等离子喷涂设备主要由等离子喷涂电源、等离子喷枪、 控制柜、送粉器装置等组成(如图 2 ) 。等离子喷涂电源是等离子射流能拭提供装置 , 其工作电流和电压是影响涂层质量的重要参数。喷枪是集所有喷涂所用的电、气、粉、水于一体的核心装置,为喷涂材料的融化、细化及其喷涂能力转换提供空间, 喷枪设计的好坏直接影响到喷涂涂层的质量及喷涂效率,这两者是等离子啖涂系统中最为关键的部件。
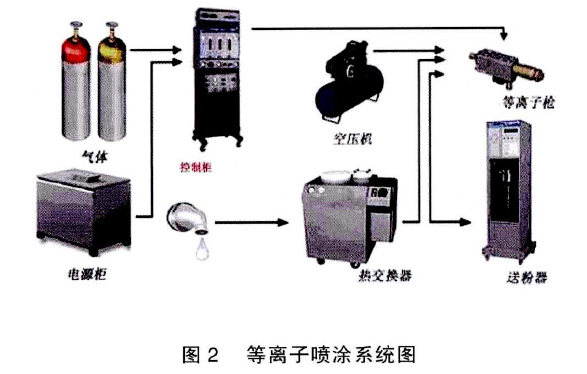
4、影响等离子喷涂制备溅射靶材效果的技术因素
4.1 电弧功率
电弧功率过高会使等离子体电离度增加,火焰温度升高, 可能会使喷涂材料气化而引起涂层成分改变。功率过低会引起粉末颗粒加热不足,涂层粘接强度低,硬度和沉积效率低。
4.2 供粉系统
供粉速度应与输入功率相适应。一般来说,粉末送到焰心才能使其获得最好的加热和最高的速度。
4.3 喷涂距离和喷涂角
喷涂材料及其涂层的特征对喷涂距离很敏感。喷涂距离过大,粉末的温度和速度下降.结合力、喷涂效率都会明显下降; 过小会使基体表面温度过高,影响涂层结合。在基体温度允许的情况下,喷涂距离适当小些为好。喷涂角,一般应大于45度.喷涂角过小会导致“阴影效应",涂层中会出现空穴,造成涂层疏松。
4.4 基体的温度控制
在喷涂前把工件预热到喷涂所需要的温度.然后对工件采取喷气等冷却措施,使其保持恒定温度。
4.5 喷涂压力
在金属材料的喷涂过程中一般采取低压等离子喷涂(也叫真空等离子喷涂),在压力为4~40 kPa的可控气氛腔室内喷涂。由于工作气体离子化后, 是在低压气氛中边膨胀边喷出 , 喷流射速可达到超音速, 适合对氧化敏感的金属材料的喷涂。对于氧化物陶瓷可采用水稳等离子喷涂,其能量密度高, 燃烧稳定, 喷涂效率高。
5、等离子喷涂制备溅射靶材中存在的问题
等离子喷涂在 溅射靶材 制备方面有着巨大潜力( 如图 3 ),但同时该方法也存在一个重要缺陷, 那就是喷涂组织的多孔性。使其制造的靶材相对密度只能达到85%~95% , 靶材纯度一般在99.5%~99.9%之间。而组织的疏松多孔, 容易吸附杂质、湿气等妨碍溅射过程中高真空的迅速获得及真空度的稳定,并且导致在溅射过程中,靶材溅射表面瞬间高温使松散颗粒团状掉落,污染被镀件表面, 影响镀膜质量和镀膜产品的合格率。另外,若在大气环境下 喷涂, 靶材表面 和空气中的O2和N2, 等气体大面积接触, 会产生大量的氧化物和氮化物杂质, 即使是真空等离子喷涂技术 ,也不能完全避免合金靶材中氧化物和氮化物的产生。因此, 喷涂靶材在溅射前必须用隔离的前级泵除去表面吸附气, 从而提高溅射速率和质量。
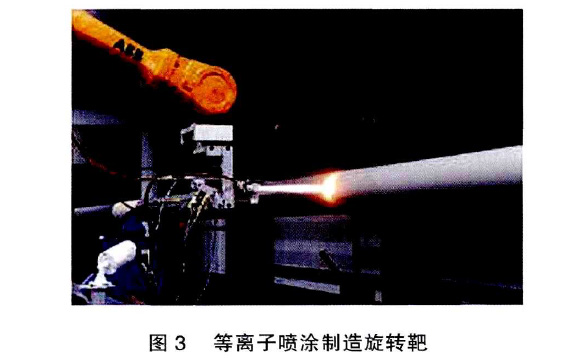
四、等离子喷涂制备溅射靶材发展趋势
等离子喷涂法仅需要更换成塑粉末和工艺参数就能够制备范围广泛的各种材料的大型平面靶和旋转靶。随着等离子喷涂技术的发展, 势必会引起溅射靶材制备技术的重大变革。目前等离子喷涂技术仍需进行以下几方面的研究 :一是合理选择喷涂工艺,优化工艺参数、 改善粉末受热和熔化状态, 减少环境对高温离子的污染和氧化, 形成性能优良的溅射靶材。二是进一步研究涂层形成机理、孔隙形成机理, 寻求消除或减少孔隙率的办法。三是进一步研究涂层与基体的结合机理,提高涂层强度。
相关链接