钛材料在高新技术产业中应用较多,这与钛金属的优势有着密切关系,比如钛的比重较小,具有较好的耐腐蚀、耐磨以及无毒优势。钛金属实际应用十分广泛,如可用于化工行业、核电行业、石油行业等,在上述相关行业领域应用期间,薄壁钛管材包含了焊接管与无缝管,无缝管与焊接管相比,在生产加工期间投入大、生产周期长、产品合格率较低, 特别是在超长管材以及超薄管材加工期间,其实际投入与产出之间存在较大差异性[1]。焊接管材与无缝管加工相比,其生产效率明显提高。下文探讨TA2 纯钛焊接管无缝化处理的相关问题。
1、问题的提出
钛管材在焊接过程中虽然较钛管材无缝化对应的生产周期、生产成本下降,且具有较高的成品率,但是焊接过程中由于焊接热力效应以及焊缝的存在,造成焊接区域组织粗大,表现出铸态组织,致使基体与焊缝位置性能差异较大,而焊缝位置也成为了整个钛管材焊接的薄弱点,对管材的安全使用以及使用寿命产生影响[2]。对于内表面存在焊缝余高问题也会引起焊材出现应力集中问题,降低管材的耐腐蚀性能,因而一般环境条件下焊接管材能够满足要求且应用广泛,但是对于环境要求较为复杂的,焊接管的实际应用受到限制,具体应用期间的安全性以及使用寿命均会受到环境条件影响。基于此,需要通过冷轧加工处理以及相关热处理将焊缝对整个基体产生的影响彻底消除或者大幅度降低,便于钛金属焊接材料应用范围的延伸。
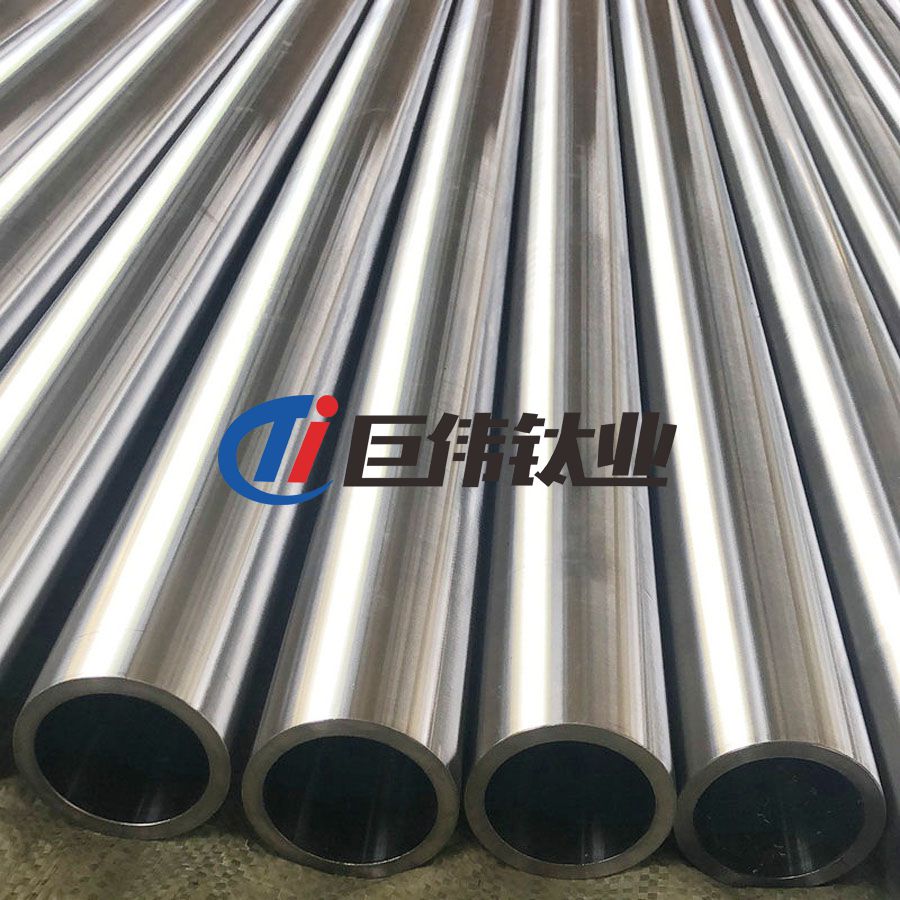
2 实验过程
2.1 坯料
焊机管材原料选择进口材料,具体为日本住友公司生产的二类纯钛带,厚度为0.7mm,分条处理后,通过自动化焊管生产线,将其加工成为焊接管,具体规格为ф23mm×0.7mm,切取3 支3000mm 的定尺,并实施涡流探伤、尺寸检查、宏观检查、水压试验等,确保其相关参数以及性能达到合格要求,经过上述处理将其作为无缝化处理坯料。
从上述制作的焊管坯料上选取5mm 高度的环形试样,细致的对选取试样横截面焊缝组织进行观察,找到管材焊缝位置后对其进行切削处理,分析其化学成分,评价焊缝中化学元素含量水平;严格按照国家行业标准,对选取的试样进行拉伸、扩口、压扁以及反向展平等操作,对管材拉伸性能以及相关参数做出处理[3]。
2.2 无缝化处理
整个无缝化处理需要按照以下流程进行:选取焊管坯料,对不同加工率管材实施冷轧处理,除油后酸洗,真空条件下退火。使用LD30 多辊冷轧管机对选取的3 支ф23mm×0.7mm×3000mm 焊接管材进行处理,冷轧处理后使其达到ф22mm×0.6mm、ф21mm×0.55mm 以及ф20mm×0.5mm 要求,对应的冷加工率为17.00%、
28.00% 以及34.00%,完成冷轧处理后,从不同规格成品中选取试样,要求从不同产品中间区域选取,环形试样的高度为5mm,获取试样后观察横截面焊缝组织,并对比不同冷轧率条件下观察结果的差异性;研究焊缝组织中完全破碎管材,并进行如下操作,包括除油酸洗与真空退火,真空退火条件为600℃ ×2h/AC,将升温速率控制在每分钟15℃。通
过上述操作完成无缝化处理。无缝化处理完成后继续选取试样,同样从处理后的试样中间位置选取环形试样,高度仍然为5mm。仔细观察管材横断面金相组织,依据标准操作方法实施拉伸、扩口操作、压扁操作以及反向展平操作,通过上述相关操作试验了解试样的力学性能以及加工处理工艺。从焊缝位置获取化学成分,然后进行试样分析,了解无缝化处理后管材焊缝区域中间隙元素情况以及含量水平等。
上述操作均由专业人员严格按照国家现有的行业法规进行处理。
3、实验结果分析
3.1 冷轧加工率的选择
图1 所示为TA2纯钛焊管以及采取不同加工措施后冷轧焊管显微组织,a、b、c、d 对应的冷加工率分别为0.00%、17.00%、28.00% 以及34.00%。观察图片,冷加工率为0 的情
况下,基体组织与焊管管材焊缝区域组织差异性明显,两者之间有着较为清晰的分界线,其中基体组织表现出等轴组织,较为细小且均匀,但是焊缝区域包含了过热的魏氏组织以及铸态组织。靠近表面的区域,晶粒较小,有针状α 相存在且数量较多,有细小的等轴颗粒存在于粗大组织区域。出现这一结果与实际焊接有关,钛管材的焊接期间,焊缝表面暴露在空气中,而焊缝中间区域受到保护,两者在焊接后冷却速率方面存在差异,这种差异造成上述焊缝区域与基体之间存在不同。金属焊接过程中的问题较高,对应的熔化以及冷却过程较为迅速,致使熔池中存在未完全液态化的排列组织,冷却后这些未完全液态化的排列组织可称为形核中心,表现出细小的等轴组织。
在冷加工率为17.00% 的条件下,通过冷轧变形,原有焊缝组织中的粗大组织发生了改变,尽管如此,焊缝区域和基体之间仍然存在较为清晰的分界线。在冷加工率为28.00%
的条件下,焊缝中的粗大组织变化明显,部分粗大晶粒发生破碎,此时基体和焊缝中间的分界线逐渐变得模糊,虽然已经发生了改变,但是仍然有粗大铸态组织的存在,局部区域
仍然有清晰的分界线,后期退火处理后,焊缝组织没有完全消除。当冷加工率达到34.00% 的时候,由于冷加工率较大,焊缝中间的魏氏组织以及铸态组织得到有效破碎,焊接过程中温度所产生的热效应得到消除,焊缝区域和基体之间融为一体,无法分辨出焊缝所在位置。也就是说通过对管壁实施减壁冷轧处理,焊接期间形成的焊缝得到了有效处理,有效的实现了焊缝消除。通过对不同冷轧率基体和焊缝关系的分析,冷轧率为34.00% 的退火处理后有焊缝完全消除的可能。
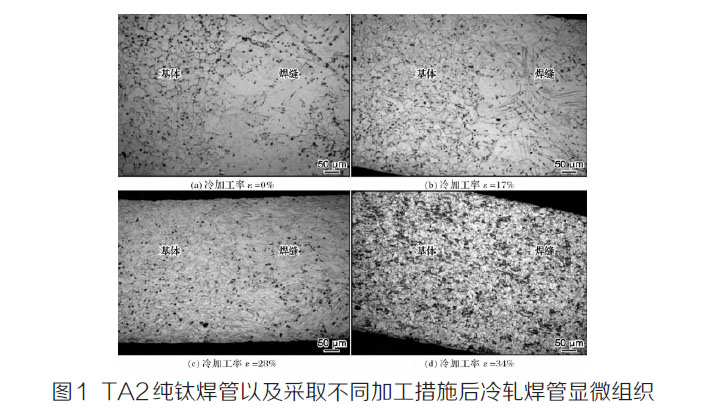
3.2 无缝化处理焊接管组织和性能
(1)无缝化处理前后间隙元素改变情况。钛管材在焊接过程中,焊接操作、真空热处理可能会造成管材中元素含量的变化,其中以焊接管间隙区域元素含量变化可能性更大,
表1 所示为无缝化处理前后焊接管材焊缝区域元素成分变化情况。从国内表中数据可以看出,无缝化处理前后间隙元素含量基本没有发生改变,且符合国标要求。分析其中氢元
素含量水平下降可能是在真空退火期间,焊缝位置的氢会随着温度升高出现流失,造成氢元素含量下降。
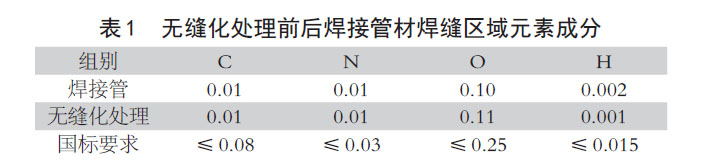
(2)无缝化处理前后显微组织变化。图2 所示为无缝化处理前后焊管显微组织表现,通过观察图中显微组织,在无缝化处理后,纯钛焊接管材对应的焊缝、热影响区、铸态组织、魏氏组织等均完全消除,基体与焊缝组织保持一致,均呈现出等轴组织,较为均匀且细小,其中粒径大小约为20μm。
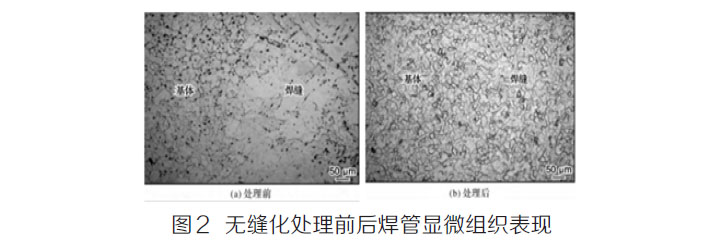
(3)无缝化处理前后拉伸性能对比。表2 所示为无缝化处理前后焊接管材拉伸性能相关参数,主要是抗拉强度、屈服强度以及延伸率。通过对焊接管实施无缝化处理,处理后
的上述参数有所提高,而经过冷轧无缝化处理后,上述参数出现较大幅度的改变,但是均符合国标中的相关要求。拉伸性能的改变与处理过程有着密切关系,通过无无缝化处理,
焊缝中间的热影响区、铸态组织、魏氏组织等均被消除,粒径均匀度较高,因而总体拉伸性能提高。
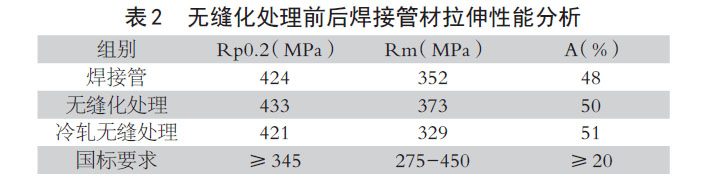
(4)无缝化处理工艺性能分析。根据规范要求,对无缝化处理后的管材进行了多项实验操作,反向展平过程中,冷轧无缝处理后的管材没有出现裂缝;展平实验过程中通过冷轧
无缝化处理,管材在展平期间同样没有出现裂缝,焊缝区域与基体均为裂缝,表明经过无缝化处理以及冷轧无缝化处理,管材的总体性能得到改善,焊缝薄弱点的应用现状得到改善。无缝化处理以及冷轧无缝化处理后,选取试样同时进行扩口试验和压扁试验,扩口后的外径超过24mm,而压扁距小于5.6mm,上述试验中,无缝化处理、冷轧无缝化处理结果较为接近,且均符合国标要求。表明采取的上述相关措施能够保证钛管材的相关性能,提高了对复杂环境下的适应能力。
4、研究结论
本研究中通过实验方法分析了钛管材、无缝化处理、冷轧无缝化处理后的相关质量,具体为焊缝区域的显微组织图以及拉伸性能。研究结果显示通过无缝化处理以及冷轧无缝
化处理,在冷轧率为34.00% 的情况下,钛焊接管材对应的焊缝、热影响区、铸态组织、魏氏组织等均消除,且拉伸性能符合要求,存在替代无缝管的可能性。
参考文献
[1] 陈火根. 无缝化技术在锦浦中桥改造中的应用[J]. 四川建材,2018,44(07):132-133.
[2] 孟梁. 谈既有线道岔无缝化施工与维修[J]. 山西建筑,2017,43(18):146-147.
[3] 张良玉, 李华, 刘守田.TA2 纯钛焊接管无缝化处理及焊缝组织和性能分析[J]. 钛工业进展,2016,33(06):32-35.
相关链接