前言
激光加工技术作为一种先进的加工手段,在现代航空航天、国防领域以及国家建设中扮演着越来越重要的角色。特别是在钛合金加工领域,2000年以后,随着高功率激光器品质的不断提升,激光焊接与激光增材制造的应用越发广泛。本文在研究国内外激光加工技术相关文献报道的基础上,对激光焊接和激光增材制造在钛合金航空结构件加工中的应用现状进行总结分析。随着航空结构件向大型整体化、构型拓扑化、结构功能一体化的不断发展,未来激光加工技术在钛合金结构件加工领域的应用场景将更为广泛,同时也对未来钛合金激光加工成套设备也提出了更高要求,不受制于人的高端激光成套制造设备将是钛合金航空结构件加工核心竞争力。
1、军机结构件制造面临的挑战及发展趋势
1.1 各代军机结构需求及材料发展
一代军机,一代材料[1]。第一代飞机主要满足高亚音速飞行,强调结构件的屈服强度、抗拉强度、塑性及冲击韧性,主要使用钢骨架和木质材料;第二代飞机主要满足高空高速、近距格斗需求,强调关键部位的疲劳性能,大量使用铝合金和钢;第三代飞机主要满足高亚声速机动性需求,关键部位的材料要求具有较高的损伤容限性能,要求材料具有
较低的裂纹扩展速率和断裂韧度,需要应用大量轻质高性能材料,在铝合金和钢的基础上,增加了钛合金与复合材料的使用;第四代飞机主要强调隐身性能和长寿命周期,注重飞机的耐久性设计,主要材料与三代机相近,但钛合金与复合材料占比更大;第五代飞机需要具备高智能、高协同、高速飞行的特性,对结构强度要求更高,还需应用大量热防护材料和耐高温合金。
1.2 军机结构件制造面临的挑战
1.2.1 减重增寿
机体结构是决定军机性能指标关键要素之一,半个世纪以来,结构技术一直在发展,结构形式已趋于“经典”[2]。如表 1 所示,国外各代战机机体结构重量占全机重量百分比不断降低,机体疲劳寿命需求在不断增长。但相较于理想结构重量,F35A超重 640 kg,F35B超重 900 kg,近期美国投入 3.5 亿美元对 162 架四代飞机进行抗疲劳结构改进。减重增寿仍然是军机结构件制造面临的主要挑战。
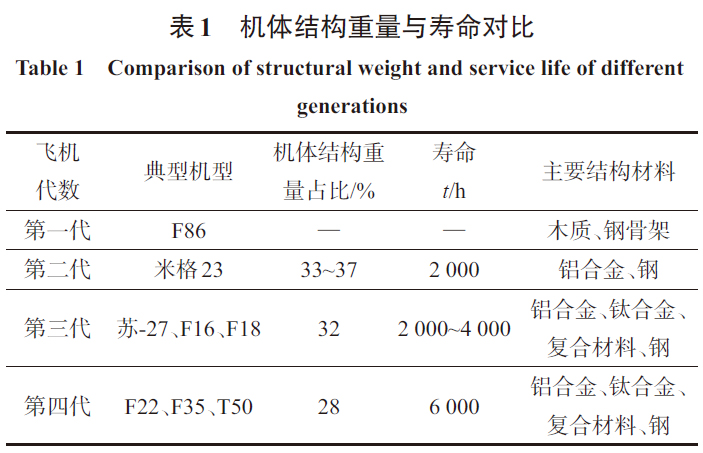
1.2.2 低成本、快速制造
快速制造和低成本制造是战机工业化生产的核心。现有的结构件制造工艺,材料利用率极低,部分结构零件材料去除率达 90%以上;复杂结构件加工工序多,生产周期长。简化制造工艺,提升加工效率,提高原材料利用率,既满足国家“双碳”发展新形势的需求,也符合航空制造业的根本利益。
1.3 军机结构件制造发展趋势
1.3.1 结构大型化、整体化
目前的机体结构采用以小拼大的方式通过连接件完成连接[3],该方式直接导致了机体结构超重,疲劳薄弱环节多,开裂频发。对于飞机结构件,将传统装配结构进行一体化设计并完成制造,既减少了结构件和连接件的数量,又能有效消除分离面,减少冗余结构,减缓应力集中,减少疲劳薄弱环节。
结构大型化、整体化设计,突破了原有机体设计极限,能够实现机体结构减重 20%以上,力学薄弱环节预计减少 30%以上,有效提升机体寿命。同时,整体化结构简化了机体装配工装与工艺,机体制造周期预计缩短30%以上。
1.3.2 结构构型拓扑化
用仿生拓扑构型代替传统的纵横加筋板构型,材料根据传力路径和功能需求布局,能将材料布置到最优传力路径,实现“无冗余”设计,进一步优化了结构设计,实现减重。图 1 为拓扑优化前后的飞机结构零件,零件质量由 0.89 kg 减至 0.35 kg,减重60.6%。
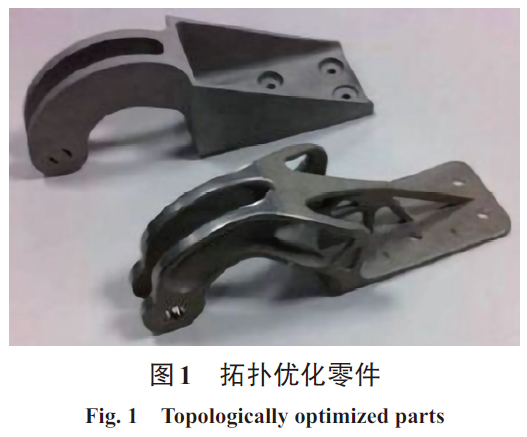
1.3.3 结构功能一体化
目前,军机的结构系统与功能系统是独立的,未来的军机会将功能系统融入结构中,取消功能系统的冗余,功能结构一体化,诸如防热材料、微结构与结构构型融合,达到耐热防热的目的,可进一步实现减重。典型防热承载一体化结构如图 2 所示。
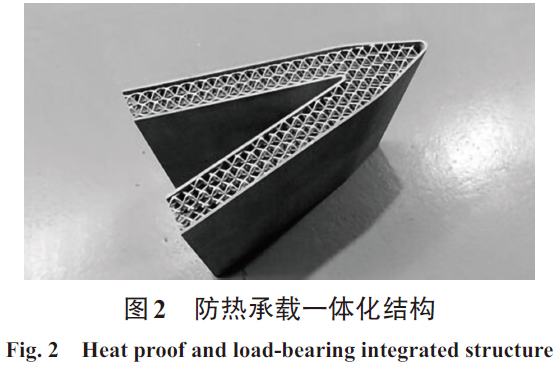
2、激光加工技术在钛合金航空结构件制造中的应用现状
2.1 激光焊接技术
激光焊接在航空结构件制造的优势主要有两点[4-5]:首先,焊接代替传统铆接,节省了大量铆钉,能有效实现减重;其次,整体焊缝的强度优于多个铆钉连接的强度。如图 3 所示,钛合金焊缝及其热影响区的强度均大于母材,整体焊缝的强度非常优秀,能够有效增长机体疲劳寿命。
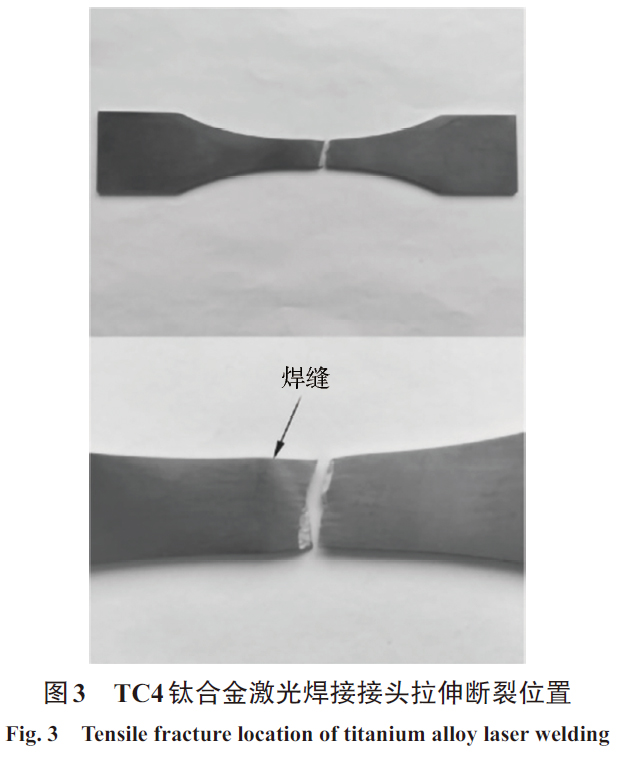
目前应用最为广泛和成熟的是T型接头双光束激光焊技术,该技术最早由空客于 2000 年应用于A318 系列飞机的下机身蒙皮焊接(见图 4),被公认为近十年大型客机制造领域的一次技术革命,改变了焊接技术不适用于飞机制造的传统观念。国内针对TC4 钛合金和TA15 钛合金激光焊接已进行了系统的研究[6-10],激光焊接已经应用于我国某些型号飞机的钛合金腹鳍制造、钛合金蒙皮拼焊、壁板与长桁T型接头焊接等,配套制造设备也较为成熟。
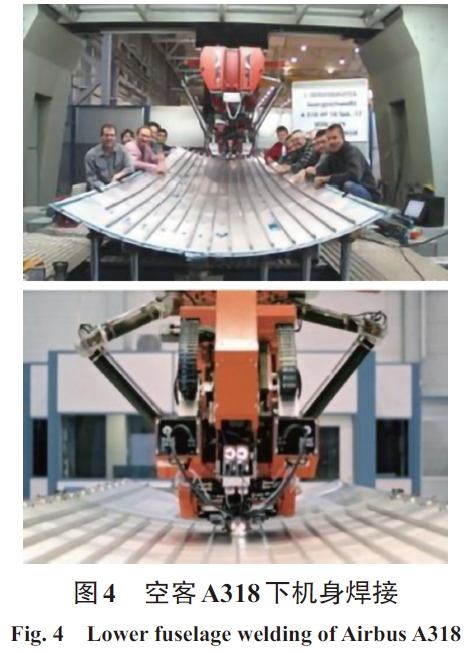
图 5 为中国商飞双光束同步焊接设备,用于国产某客机制造。此外,北京航空制造工程研究所已将激光焊接技术应用于发动机钛合金承力构件制造。
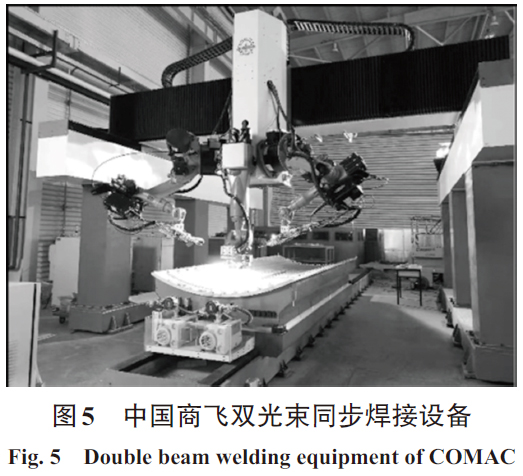
在钛合金承力结构件上,激光焊接技术即将开展深入应用,特别是钛合金原位激光焊接。原位焊接技术属于近净成形技术领域,是指零件成型后,仅需少量加工或不再加工,就可作为机械构件的成型技术。原位焊接技术是美国首次在 F-22 战机上提出并应用的,利用高能束流对装配体实施焊接,焊接后无需进行二次机械加工,实现了飞机骨架零件原位焊接工艺与装配技术的协调统一,代替传统铆接,大幅减重并缩短部件制造周期。F-22 在研发阶段,受制于当时激光功率,钛合金后机身大量采用电子束焊接。先由 3~4 个片段纵向焊接组成盒状段,再由盒装段焊接成框,最后焊接为整体舱段,如图 6 所示,钛合金焊缝总长度约 9m,质量相比于机械连接减少 182 kg[11]。目前,原位焊接技术在国内
航空制造领域尚无工程应用,钛合金结构件的原位激光焊接的应用将是未来极具价值的研究方向。
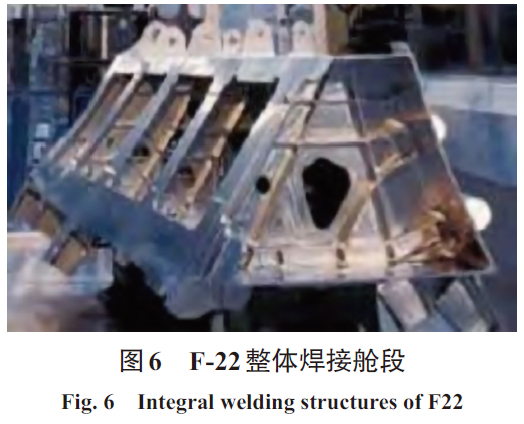
未来,激光焊接在航空结构件制造领域的发展趋势,是焊接更为复杂的机体结构和新材料,进一步实现机体减重增寿。此外,航空结构件自身价值较高,保证加工质量至关重要,由此带来的挑战主要有以下几个方面:
(1)激光焊接头可达性拓展。
复杂钛合金机体框架结构的定位和夹持工装相互交错,对激光焊接头的可达性造成极大干扰。
一方面,需要合理规划焊接路径,优化工装设计,保持操作空间的最大开敞性。另一方面,需要开展专用焊接头的研发,具备小型化、远距焊接、末端位姿可调等要素。
(2)变形控制。
变形控制包括焊接变形控制和热处理变形控制。需进一步开展焊接对象焊接工艺试验,完成最佳的焊接策略匹配,实现焊接变形控制最优解的同时保证焊接可靠性。需要进一步开展热处理变形机理研究,设计出合理的保形工装和热处理策略来实现复杂部件的热处理变形控制。此外,还需要探索新型的热处理方式,诸如超声冲击、激光冲击等特种工艺来消除焊接应力。
(3)新材料焊接。
针对未来超高速飞行器对耐温材料的需求,需进一步开展高温钛合金和热塑性复合材料的激光焊接工艺研究,并进行力学性能和疲劳性能考核,为后续新材料工程化应用提供支撑。
2.2 激光增材制造技术
激光选区熔化(Selective LaserMelting,SLM)、激光直接沉积(Laser MeltingDeposition,LMD)是目前主要的钛合金激光增材制造工艺[12]。航空结构件具有多品种、小批量的特点,结构越复杂,增材制造的成本和效率优势相比传统制造方法就越明显。
SLM技术分层层厚较小(30~60 μm),可直接快速成型终端金属产品,尺寸精度高,表面质量好,可实现任意复杂零部件的高效致密成形,特别适合内部有复杂异形结构且用传统方法无法制造的复杂零部件。
通用电气公司专注于增材制造以降低其发动机制造成本,采用SLM技术已完成大量零部件的批量制造。图 7 为航空发动机燃油喷嘴,将 20个零件集成为 1 个部件进行打印,减重 25%,已实现数万个部件的批量制造。此外,空客通过基于有限元分析的结构优化应用于现有零部件的再设计,采用SLM技术实现了大幅减重,如图8所示。
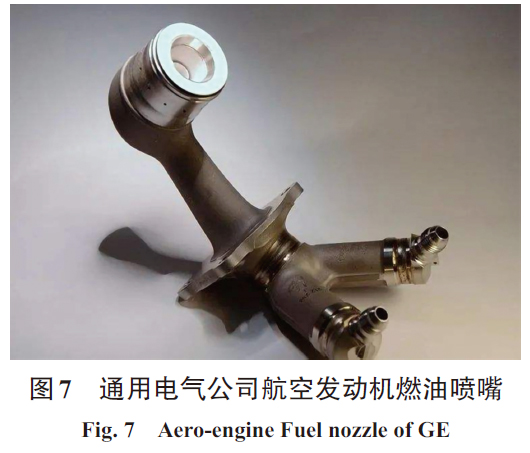
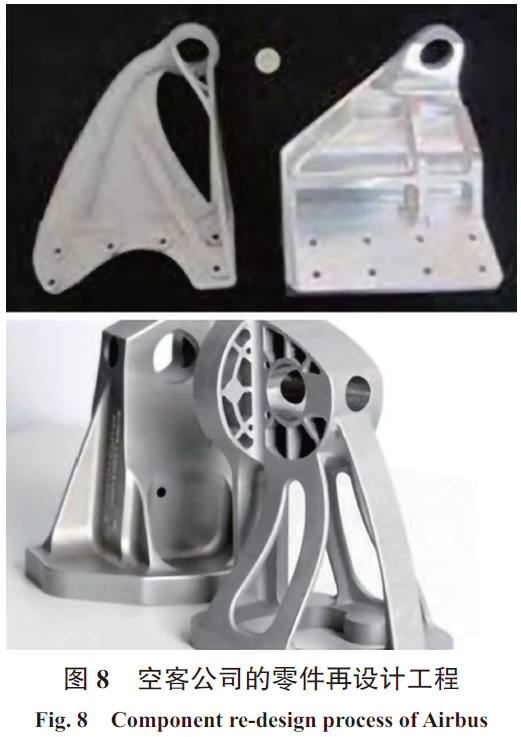
未来军机将具有超高速飞行的特征,热防护技术是未来飞机结构件的关键技术之一,防热承载结构具有多孔、点阵等特征,且内部需要微流道完成主动散热,此类结构传统工艺无法完成加工。通用航空公司设计的内置流道的航空发动机叶片如图 9所示,飞机用金属多功能点阵结构如图 10 所示,可实现结构承载、防热、隐身等功能的融合。此类结构传统工艺无法完成加工,SLM技术恰好能够满足相关制造需求。
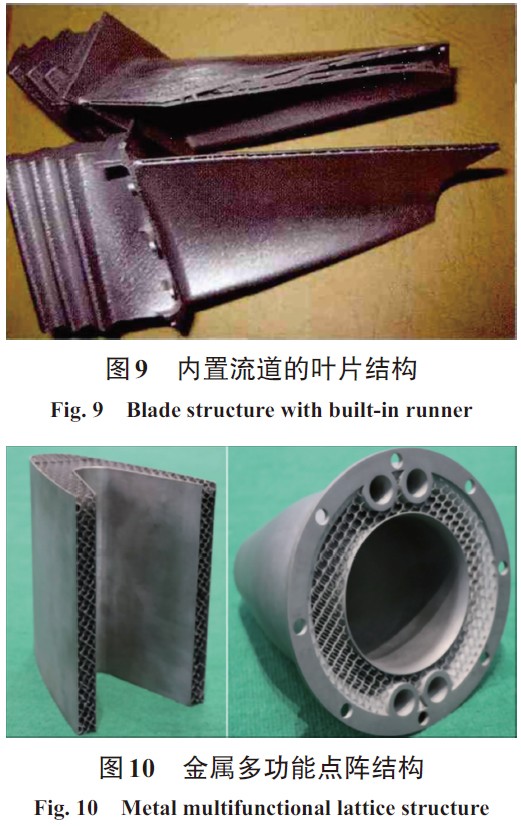
钛合金防热承载一体化结构的激光选区熔化成型应用将是未来极具价值的研究方向。
在 SLM 设备制造领域,以美国 Optomec、德国EOS、西安铂力特、南京中科煜宸等为代表的多家单位均已研发出工业级 SLM 设备,国内外典型 SLM设备主要特性如表2所示。
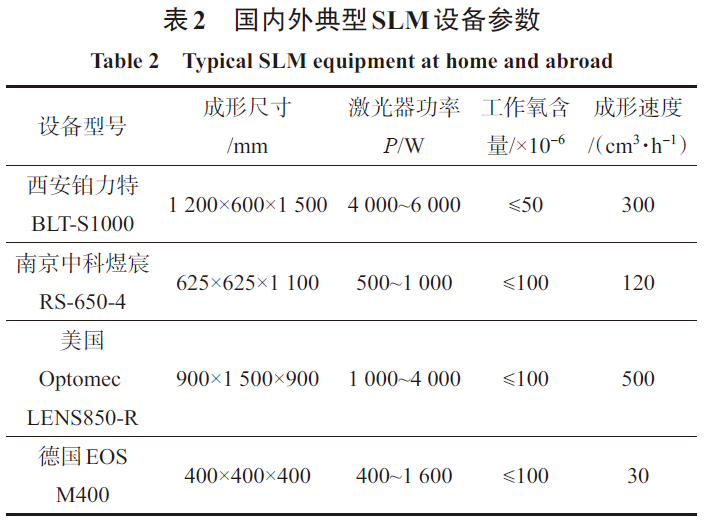
其中,西安铂力特增材技术股份有限公司于2022 年 5 月 推出了 12 激 光 SLM 3D 打 印机 BLT-S1000,目前处于国内领先水平,如图 11 所示。其成型尺寸可达1200 mm×600 mm×1 500 mm,可实现大尺寸复杂结构件的一体成型,最大成型速率可达300 cm3/h。提升铺粉设备的加工效率仍将是未来极具价值的研究方向。
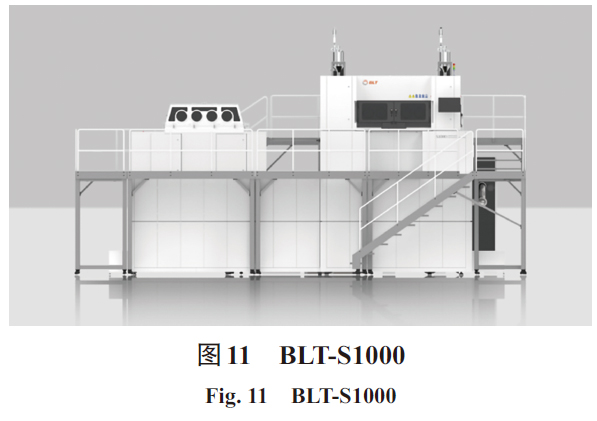
激光直接沉积技术(LMD)具有材料利用率高、机加工量小、制造周期短的特点,同轴送粉的工艺特点决定其成形尺寸不受限制,可以实现同一构件上多材料的复合和梯度制造,适用于大型结构件或者结构不是特别复杂的功能性零件的加工制造。
LMD技术在国内外航空航天领域得到了广泛的应用,例如波音公司、空客公司、洛克希德马丁公司、GE航空等世界著名的航空公司都在大力发展各自的激光直接沉积技术[13]。北京航空航天大学研制的某大型激光直接沉积金属增材制造设备如图 12所示,可为中国商用飞机、军机项目制造大型复杂部件,包括钛机身骨架及高强度起落架。北航王华明教授团队研制了主承力飞机钛合金加强框等关键构件,实现了在包括C919 大型客机在内的多种型号飞机上的装机应用。北航应用LMD技术制造出了飞机大型钛合金主承力构件,如图 13 所示。西北工业大学采用LMD技术成功试制了C919 机翼肋构件,如图14所示。

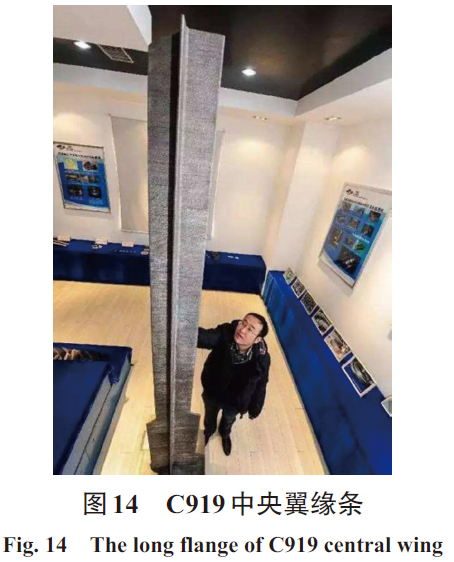
在LMD设备制造领域,以美国 EFESTO、德国EOS、西安铂力特、南京中科煜宸、鑫精合激光等为代表的多家企业均已研发出工业级LMD设备,国内外典型LMD设备主要参数如表3所示。

南京中科煜宸研发的大型智能化双光束装备性能指标达到国际先进、国内领先的水平,如图 15所示,是国际上首次提出采用双万瓦级激光同步送粉打印技术,沉积速度可达 700 cm3/h,设备刚性成型尺寸可达 4 m×3.5 m×3
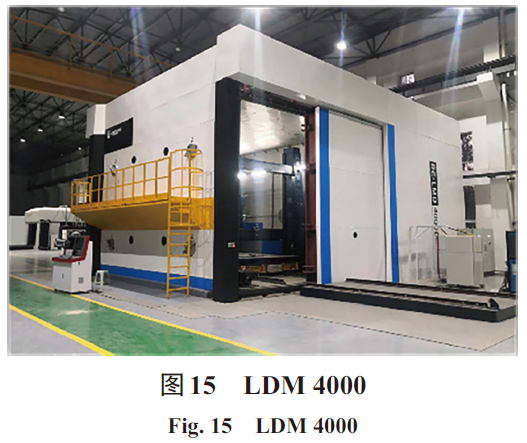
m,柔性成型尺寸达 13 m×3.5 m×3 m,加工能力覆盖了目前航空钛合金主承力结构件的所有门类,满足未来型号及特殊构件制造需求。此外,航空工业成飞集团也研制了大型LMD同轴送粉设备,并实现了飞机增材制造工程化应用。降低设备加工使用成本将是LMD设备未来的研究方向。大型构件的应力控制和变形开裂是LMD技术面临的关键难题。
激光增材制造在航空结构件制造领域的未来发展趋势,将是进一步拓宽应用面,提高零部件力学性能,加工对象将由机体非承力件和次承力件向主承力件进一步拓展。同时,进一步提升加工工艺成熟度,降低加工成本,更有助于该技术的工程化应用。由此带来的挑战主要有以下几个方面:
(1)提升正向设计能力。
目前,增材制造技术主要还是对传统铸造、锻造技术的替代,没有完全发挥其高设计自由度的优势,需要进一步提升结构件设计能力,在设计中融合增材的思想,通过正向设计的理念,从源头上实现结构设计上的颠覆性创新。
(2)提高零件力学性能。
激光增材制造的关键要求之一是获得所需的力学性能,需要进一步优化打印工艺,减少变形,避免开裂,提高力学性能。一方面,需要开展大量的基础性试验,建立工艺数据库;另一方面,需要开发可靠的预测性过程模型,诸如过程热模型、微结构预测模型和力学性能预测模型等,提升加工过程的可靠性。
(3)健全基础性能数据体系。
作为一项正在迅速发展的高新技术,增材制造在原材料、工艺、后处理、组织性能数据库等方面的数据储备还不充足,需要业界共同努力,健全激光增材制造金属材料的基础性能数据体系,共同开发出增材制造粉末原材料、工艺过程等规范。
3、激光加工设备在钛合金航空结构件制造的应用展望
伴随着钛合金激光加工技术在我国航空结构件制造中的应用越来越广泛,钛合金激光加工成套设备同样面临着压力与挑战,需要进一步完善和发展,提升激光加工设备竞争力。
3.1 成套系统多功能化
高效低成本制造、近净成形将是未来钛合金航空结构件制造发展方向。航空工业属于典型的离散制造,现行的工艺以及加工设备大多仅具备单一的加工功能,零件在不同的工艺节点周转,降低了加工效率。单个离散点多功能化,简化工艺流程,需要未来的高端激光制造集成系统向多功能化发展,将激光制造精细、直接近净成形的优点与传统制造技术结合起来,形成最佳的制造策略,诸如增材、焊接、减材、在线测量一体化的自动设备。同时,研发面向原位自适应制造的专用新设备,诸如在线焊接变形测量和分析设备、在线焊接气孔检测设备、原位去应力设备,可有效减少后续加工及检测工序。
3.2 加工过程智能化
智能化的激光加工系统将有效提高加工效率,保证加工质量,降低对操作人员的要求。将智能传感器、数字总线技术等智能部件融入激光加工设备,通过对生产全过程实时在线检测、闭环过程控制来确保激光加工的加工质量、一致性和再现性。
诸如基于视觉测量、激光测量的智能末端,完成部件装配的间隙与阶差的自动测量,确保装配状态,代替现有人工测量;高精度的远距窄焊缝的焊缝跟踪末端,满足航空结构件形状复杂、夹具复杂、焊接末端可达性较差的特殊焊接场景需求;具备高温加工全过程监测并结合 AI 深度学习功能的熔池监测设备,实现过程中的关键工艺参数和在线实时监测、反馈闭环控制;另外,构建激光加工知识工程,形成激光加工设备技术管控平台,也能有效提升激光加工的可靠性及智能化程度。
3.3 配套系统高效化
钛合金在高温下非常活跃,在 300 ℃以上极易与氢反应,600 ℃以上极易与氧反应,700 ℃以上极易与氮反应,须施加氩气保护,高质量的气体保护措施能有效保障钛合金加工质量,提升零部件制造合格率并降低加工成本。对于传统保护夹具吹气的方式,需注重其保护的可靠性,同时需降低对光束可达性的影响;对于整体密封保护的方式,需进一步提高箱体密封性,优化惰性气体置换和净化过程气流组织,降低惰性气氛建立时间,提高加工效率。
3.4 核心部件自主化
经过多年的不懈努力,我国激光制造设备已实现“从无到有”,目前正处于“从有到好”的阶段。但部分高端核心部件目前仍然处于受制于人的局面,急需研发高功率、高可靠性的国产激光器,并针对性地改善功率衰减过快的缺点。研发高功率、高精度、高可靠性国产激光焊接头/打印头,在线熔池监测装置等核心部件,提升高端激光成套制造设备的
自主化程度。
4 、结论
以航空结构件制造为背景,介绍了航空结构件制造面临的挑战与发展趋势,综述了激光加工技术在钛合金航空结构件制造中的应用现状,并对钛合金激光加工成套设备的未来发展方向提出了相关建议。
(1)分析了军机结构件制造面临的挑战和发展方向。
(2)介绍了激光焊接技术、激光增材制造技术在飞机结构件制造中的应用现状及前景,对激光技术在军机结构件制造的应用具有指导价值。
(3)基于未来军机快速、高效、低成本制造的考虑,对未来钛合金激光加工成套设备技术的发展,提供了方向和发展建议。
参考文献:
[1] 李航航,阎勇,尹航 . 战斗机新结构应用与新材料需求分析[J]. 航空科学技术,2020,31(4):8-13.
Li Hanghang,YanYong,YinHang. New structureapplication andnewmaterialrequirementanalysisfor fighter aircraft[J]. Aeronautical science&Technology,
2020,31(4):8-13.
[2] 刘文珽 . 结构可靠性设计手册[M]. 北京:国防工业出版社,2008.
[3] 李蒙,凤伟中,关蕾,等 . 航空航天紧固件用钛合金材料综述[J]. 有色金属材料与程,2018,39(4):53-57.
Li Meng,Feng Weizhong,Guan Lei,et al. Review ontitanium alloymaterialsforaerospacefasteners[J]. Nonferrous MetalsMaterialsandEngineering,2018,39
(4):53-57.
[4] 许平,毕世权,张伟宁,等 . 激光焊接大型整体壁板设计与考核方法[J].飞机设计,2021,41(04):49-55.
XU Ping,BI Shiquan,ZHANG Weining,et al. Design and assessmentmethodoflaserweldedlargeintegral panel[J]. Aircraft Design,2021,41(04):49-55.
[5] 孙文君,王善林,陈玉华,等 . 钛合金先进焊接技术研究现状[J]. 航空制造技术,2019,62(18):63-72.
SUN Wenjun,WANGShanlin,CHEN Yuhua,et al. Development ofadvancedweldingtechnologiesfortitanium alloys[J]. Aeronautical ManufacturingTechnology,
2019,62(18):63-72.
[6] 李昊,陈洁,陈磊,等 . 双光束激光焊接技术在民用飞机上的应用现状及发展[J]. 航空制造技术,2012,55(21):50-53.
LI Hao,CHEN Jie,CHEN Lei,et al. Existing stateand development onduallaser-beambilateralweldingtech‐nology usedincivilaircraft[J]. Aeronautical Manufacturing Technology,2012,55(21):50-53.
[7] 龚时华,郑忠香,王平江,等 . 十轴六联动双光束激光焊接及其跟踪控制技术[J]. 航空制造技术,2018,61(11):34-39,47.
GONG Shihua,ZHENG Zhongxiang,WANGPingjiang,et al. Control technologyfordual-beamlaserwelding andseamtrackingwithten-axissix-linkageCNC
[J]. Aeronautical ManufacturingTechnology,2018,61(11):34-39,47.
[8] 蒋志伟,龚时华,王启行 . 双光束激光双路焊接的跟踪控制技术研究[J].激光技术,2013,37(1):1-5.
JIANG Zhiwei,GONG Shihua,WANGQihang. Study on thetrackingcontroltechnologyofdual-beamlaser welding[J].Laser Technology,2013,37(1):1-5.
[9] 梁斌焱,许先雨,龚时华,等 . 三维 T 形焊缝的双光束焊接及其焊缝跟踪控制[J]. 焊接学报,2016,37(2):47-50,131.
LIANG Binyan,XU Xianyu,GONG Shihua,et al.Dualbeam laserweldingandseamtrackingcontroltechnology for 3D T-beam[J]. TransactionsoftheChinaWelding
Institution,2016,37(2):47-50,131.
[10] 曹田野,徐志刚,王亚军 . 双光束激光焊机研究与设计[J].电焊机,2016,46(1):40-44.
CAO Tianye,XU Zhigang,WANGYajun,et al. Research anddesignontheduallaser-beambilateral welder[J]. Electric WeldingMachine,2016,46(1):
40-44.
[11] 李志强,陈玮 . 高能束流加工技术在航空领域的应用进展[J].航空学报,2022,43(04):54-66.
LI Zhiqiang,CHEN Wei.Application progressofpower beam processingtechnologyinaeronauticalindustry [J]. Acta AeronauticaetAstronauticaSinica,2022,43
(04):54-66.
[12] 林鑫,黄卫东 . 应用于航空领域的金属高性能增材制造技术[J].中国材料进展,2015,34(9):684-688,658.
LIN Xin,HUANG Weidong. High PerformanceMetal Additive ManufacturingTechnologyAppliedinAviation Fifield[J]. Materials China,2015,34(9):684-
688,658.
[13] 朱忠良,赵凯,郭立杰,等 . 大型金属构件增材制造技术在航空航天制造中的应用及其发展趋势[J]. 电焊机,2020,50(1):1-14,124.
ZHU ZhongLiang,ZHAO Kai,GUO LiJie,et al. Application anddevelopmenttrendofadditivemanufacturing technologyoflarge-scalemetalcomponentinaerospace
manufacturing[J]. Electric WeldingMachine,2020,50(1):1-14.
相关链接