在飞机及发动机结构中,承力、传力结构的重要件和关键零件一般需要进行锻造⑴。航空钛锻件在锻压行业中属于技术含量最高、质量要求最严、价格最为昂贵的一类锻件⑷。其中大型航空锻件所用材料和成形技术是彰显国家综合国力的标志之一。
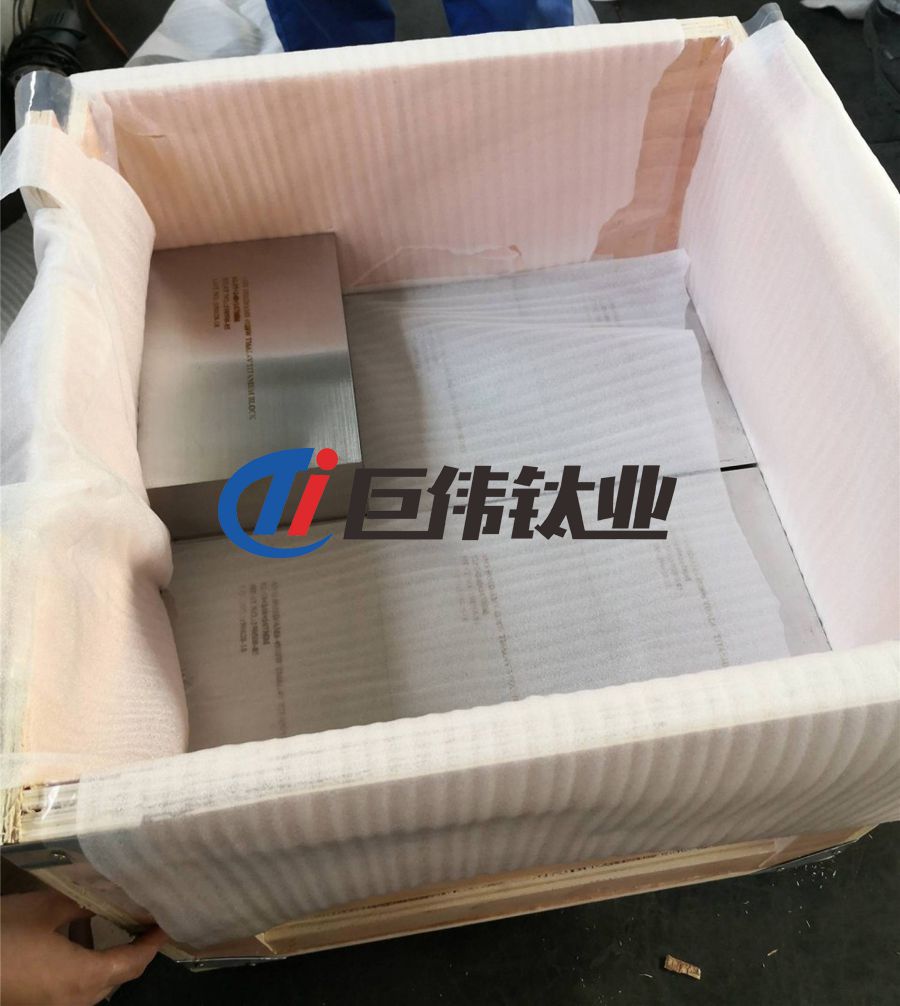
1、大型航空锻件材料应用现状
航空锻件一般选用高比强度、比刚度的材料,大型航空锻件用材料主要包括钛合金、超高强度钢、铝合金三大类。
1.1 大型航空锻件用钛合金
钛合金由于其高比强度、比刚度、耐蚀性等优异性能,在航空工业得到了广泛的应用,对飞机结构减重和零件的使用寿命提高都有显著效果⑶。特别是对于军用飞机,一些重要的结构部件如翼梁、隔框、起落架等广泛采用钛合金锻件加工而成,单件重量高,尺寸和截面积大。例如波音B747飞机主起落架支架梁8个件号采用TibAbV钛合金锻件,单件重1724kg,长度6.2叫投影面积4.1m2。空客A380飞机两个六轮三轴小车式主起落架载重梁采用Ti-1023钛合金锻件,长4.255m,重量3210kg。美国洛克希德公司研发的第四代战斗机F22隔框采用TibAobVELI锻件,单件重量达771kg以上,投
影面积4.06m?⑷。目前航空用钛合金主要牌号有TC4、TC18、TC21、TA15、TB6(美Ti-1023合金)等。其中TC18由于淬透性最大,适合制造大型锻件,目前国内应用最多。俄罗斯根据波音和空客等民机需求,在TC18合金基础上,通过降低易偏析元素Fe的含量,开发了Ti-55531钛合金。Ti-55531强度较高,而且具有优越的淬透性和更宽的加工窗口,目前已在A380飞机吊挂接头和起落架支柱等零件上使用,国内C919飞机也开展了国产材料研制工作,国内重型直升机也正在利用此材料研发大型直升机桨毂中央件。目前收集到的数据表明:Ti-55531与TC21、TC18相比,抗拉强度较高,塑性和断裂韧性较低,但Ti-55531在=11MPa-条件下的抗裂纹扩展能力明显优于TC21和TC18合金,说明其裂纹萌生寿命较长,疲劳极限较高,适合长寿命设计。
1.2 大型航空锻件用超高强度钢
室温条件下抗拉强度大于1400MPa、屈服强度大于1200MPa的钢称为超高强度钢,通常还要求具有良好的塑韧性、优异的疲劳性能、断裂韧性和抗应力腐蚀性能。航空用超高强度钢主要用于起落架、传动齿轮、主轴承和对接螺栓等关键构件⑹。中国于20世纪50年代初研制成功30CrMnSiNi2A超高强度钢,抗拉强度为1700MPa。20世纪70年代初,结合中国资源条件,研制成功32Si2Mn2MoVA和40CrMnSiMoVA钢。1980年以来,从国外引进新技术,采用真空冶炼新工艺,先后研制出34SMMnCrMvVA(406A)、35CrNMMoA、40CrNMSiMvVA(300M)和18Ni马氏体时效钢。超高强度钢的研发为中国航空工业发展打下了坚实基础⑷。随着超高强度钢的不断研究发展,大型航空锻件用超高强度钢主要有以下几个发展方向:
(1)2200MPa级以上超高强度钢。在保证强度的前提下,塑性、韧性、疲劳性能、裂纹扩展速度和抗应力腐蚀等综合性能优于广泛应用的300M钢水平。(2)超高强度不锈钢,作为下一代舰载飞机起落架的备选材料。(3)低成本超高强度钢,用于性能要求不高的场合,例如民用飞机、大型无人机等。
1.3 大型航空锻件用高强度铝合金
铝合金由于具有密度低、比强度高、耐腐蚀性好、塑性和加工性能好、成本低等一系列优点,在航空方面一直是飞机机体结构的主要材料之一岡。当今世界各国航空锻件用铝合金主要是2XXX系(2024、2224、2324、2424、2524等)和超高强度系的7XXX系(7075、7475,7050,7150,7055、
7085等)o2XXX系铝合金属于Al-Cu-Mg系合金,被称为高强度硬铝,是用途最广泛的铝合金之一,抗拉强度为400~500MPa,比7XXX系铝合金的室温强度低,但耐热性、疲劳特性,特别是抗疲劳裂纹扩展性都优于7XXX系铝合金。典型代表2124广泛应用于F22、F35的主体结构。7XXX系铝合金属于Al-Cn-Mg-Cu系合金,这类合金具有高的比强度和硬度、较好的耐蚀性和较高的韧性、优良的加工性能。典型代表是7050铝合金,在大型航空锻件方面主要用于加强框、承力梁及接头等主承力结构⑼。我国通过微合金化以及热处理制度等方式研制了7A85铝合金,与国外7085铝合金性能相当。
7A85铝合金较7075、7175、7050合金大幅度提高了Zn的含量,降低Mg的含量,并对Fe、Si等杂质元素含量进行了严格的控制,使得7A85合金在保持较高强度水平下,还具有韧性好、疲劳强度高和抗应力腐蚀性能好等优良综合性能。与7050M7452锻件比较,7A85锻件具备了更高的淬透性,淬透层深度可达到305mm,而7050淬透层厚度为203mm,更适合制造厚大截面航空零件。国外7085合金已在大型民用飞机A380客机的机翼主梁、肋等结构获得成功应用,该机翼主梁长6.4m、宽1.9叫重达3.9t,是目前世界上最大的铝合金锻件之一。
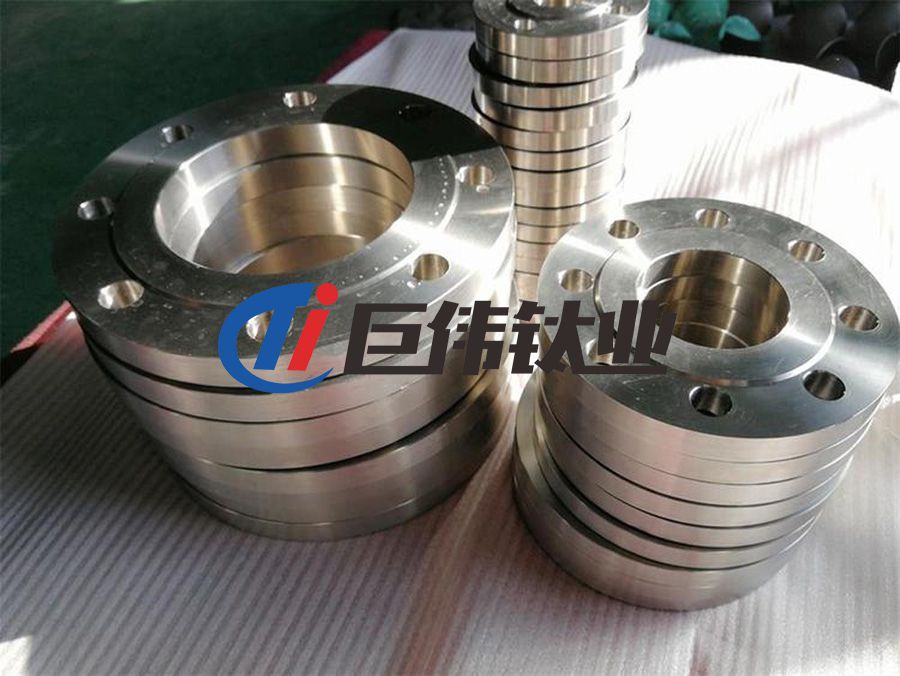
2、大型航空锻件成形技术应用现状
大型航空锻件成形技术主要包括等温锻造、多向锻造和普通热模锻锻造「冋。因等温锻造、多向锻造受外部客观约束条件较多,未在国内广泛应用,因此,本文主要介绍普通热模锻锻造技术。
20世纪60年代至90年代,国内主要设备为锤击设备,如1MN对击锤、0.4MN对击锤、0.16MN锤、0.10MN锤、0.05MN锤等⑴],围绕设备原锻造主要是靠传统经验及试错方式进行生产分段锻件(锻件长度不超2m,投影面积小于0.7m),即设计1套模具靠多火次小变形来制造锻件,首批试制如成形不足和性能不满足要求,再通过修模进行二次或多次试制,直到满足要求为止,该方式锻件余量大、制造周期长、制造成本高。进入21世纪,国内出现以800MN大型模锻压机为代表的大型锻压设备,同时配合数值模拟技术,锻造技术进入快速创新迭代阶段,锻造技术进入“可预测、可创新、可重复、可追溯”四可阶段,即技术人员用可控压机设备和数值模拟软件可提前预测锻件成形和组织性能预判,精化锻件余量,缩短了生产周期,降低了制造成本,并进一步提高了锻件质量氏。形成了短流程绿色形性协同成形技术,并取得了一系列关键核心技术。
(1) 提出了超大规格钛合金整体锻件短流程
模锻成形工艺新思路:以组织缺陷抑制与均匀流变的制造能场为边界条件,采用整体化设计及多套模具工装制造,整体框锻坯采用短流程制造,将传统制造的锻坯火次大大减少,火次减少50%左右,见图1。
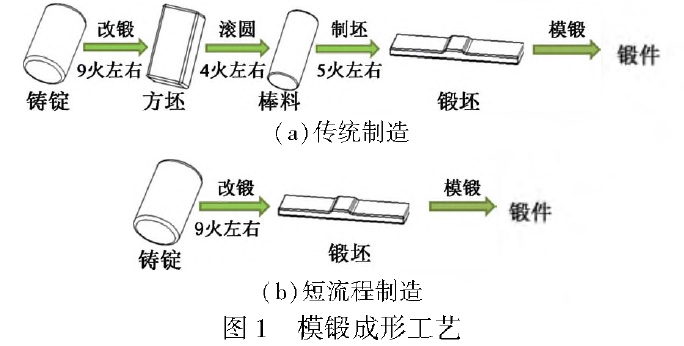
(2) 研发出钛合金锻件保温及控温分流成形
技术、大型整体锻件挤压扩孔降压成形技术、锻件局部变形死区改善及变形均匀分配技术、大型简易制造绿色长寿命堆焊模具,发明毛坯制坯件外形简化设计匹配模锻变形控制技术。
(3) 大型整体锻件挤压扩孔降压成形技术
通过优化设计制坯件,降低制坯件内孔连皮、外廓飞边材料消耗,并匹配制坯件和预锻件,巧妙运用“力的分解”,实现在预锻压制初始阶段制坯件心与预锻模具中&接触时,产生水平分力,该力挤压推动整体框制坯件孔部快速向外侧整体移动,内孔高效扩孔;预锻压制后期阶段再通过压薄制坯件乩进一步提供坯料,保证预锻件充满成形。最终实现料工比由2~2.5降低至1.6~2.1,提高每火次的变形量及变形均匀性、过程的可控性
和一致性,成型示意图见图2。
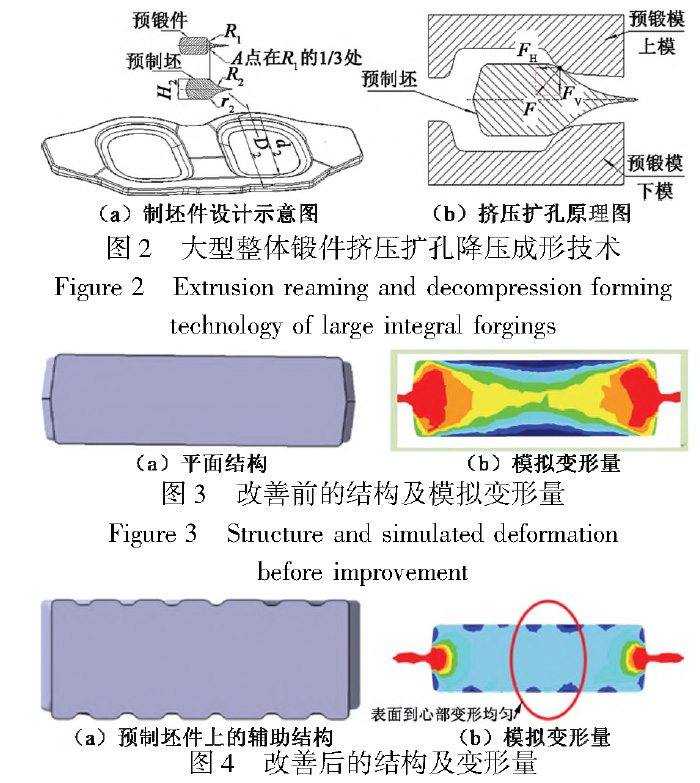
(4) 锻件局部变形死区改善及变形均匀分配
技术:通过在预制坯件上下表面或工装模具中设计R凹槽、点阵凹槽、凸R体、波浪型等辅助结构,可改善锻件表面变形死区,提高锻件表层变形量与锻件变形均匀性,锻件本体应变由0.1~0.6变为0.2-0.4,保证了锻件组织性能均匀性,改善前后示意图见图3、图4。由图可见,改善前变形不均匀,表面变形小,心部变形大;改善后表面到心部变形均匀。
3、结语
大型航空钛合金锻件中有相当数量的关键零件,例如飞机主起落架、起落架活塞套筒、飞机大梁等,都是关系飞机可靠性与寿命的重要零件,必须严格控制材料质量和锻造工艺。因此,必须根据不同材料特点,结合企业锻造设备能力的实际情况,开发出相适应的锻造工艺,并与飞机的特定需求相结合,才能发挥出最大的技术优势,助力中国航空工业的发展。
参考文献
[1]彭玲玲.航空工业需要协调发展—访中国工程院院士冯培德[J].中国科技奖励,2011(10):33-34.
[2]李凤梅,王乐安.大型模锻件与航空工业[J].新材料产业,2011(8):43-45.
[3]蔡建明.我国钛合金材料及锻件的研究与发展(上)[J].锻造与冲压,2020(11):20-27.
[4]金和喜,魏克湘,李建明,等.航空用钛合金研究进展[J].中国有色金属学报,2015,25(2):280-290.
[5]聂宏,魏小辉.大型民用飞机起落架关键技术[J].南京航空航天大学学报,2008(4):427-432.
[6]胡春东,孟利,董瀚.超高强度钢的研究进展[J].材料热处理学报,2016,37(11):178-182.
[7]赵博,许广兴,贺飞,等.机起落架用超高强度钢应用现状及展望[J].航空材料学报,2017,37(6):1-6.
[8]李成功,付志恒,于翘.航空航天材料[M].北京:国防工业出版社,2002.
[9]刘兵,彭超群,王日初,等.大飞机用铝合金的研究现状及展望[J].中国有色金属学报,2010,20(9):1705-1715.
[10]张方,窦忠林,邹彦博.航空锻造技术的应用现状及发展趋势[J].航空制造技术,2015(7):60-63.
[11]蒋鹏.我国锻造技术装备60年的进步与发展(上)[J].金属加工(热加工),2010(11):1-4.
[12]刘民德.国产大型航空模锻件挺进国际市场[J].中国设备工程,2019(24):4.
相关链接